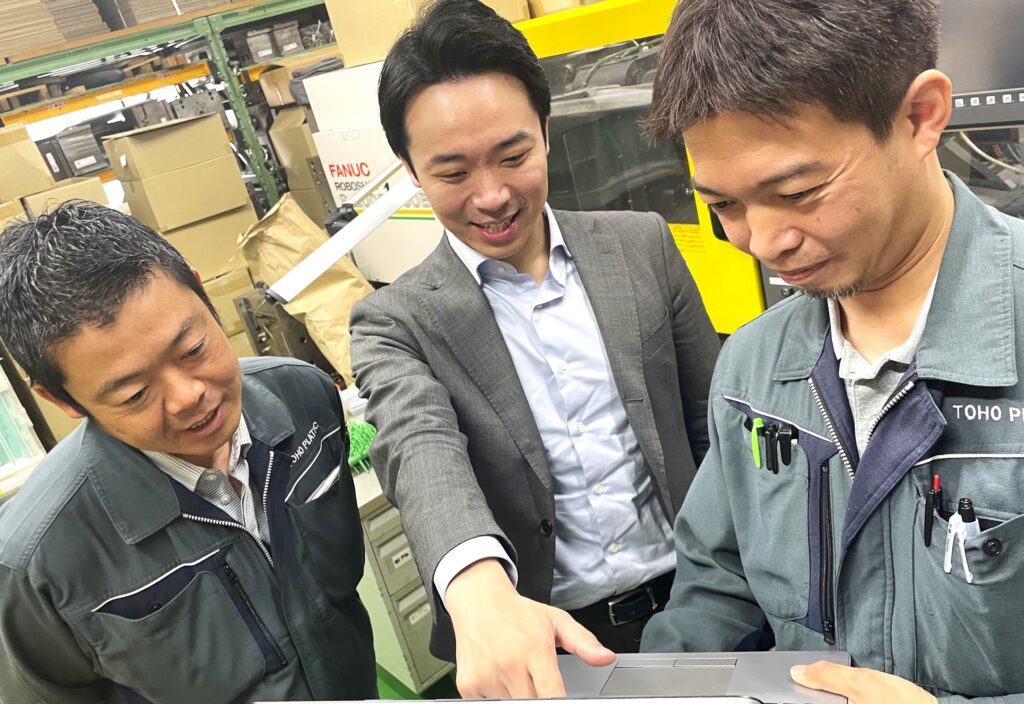
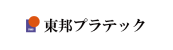
- 企業概要
- プラスチック射出成形加工企業
- 企業規模
- 20名-50名
課題・導入背景:製品在庫・材料在庫・工程管理などを一元管理したい
質問①導入に至るまでの課題や背景についてお聞かせください
三枝様:当社では従来「工程管理」や「製品在庫管理」などを、合計6シートのエクセルでマクロを組んで管理していました。シートはそれぞれ機能してるものの連動はできておらず、抜け漏れも起こりえる状況で、見直してヒヤリとすることもありました。今回導入するにあたっての最優先事項は、上記管理を1つにまとめること、そして新たに材料管理も加えて一元化したいと考えていました。
吉元:複数のエクセルをマクロ組んでの管理という弊社のお客様は多く、Sotas工程管理はこの”連動性”というのにこだわって作り続けてきましたので、そこにご興味を持っていただくことができて大変嬉しいです。
三枝様:また現状では管理者は私なのですが、管理全体が属人的な運用になっていました。他のメンバーはエクセルの仕組みについて詳細までは理解できておらず、その部分についても将来的な懸念がありました。今回の導入でその部分をクリアにして、管理者だけでなく全員で共有できる現場環境を目指しました。
Sotas工程管理に決めた理由:現場へのなじみやすさが第一優先
質問②Sotas工程管理を選ばれた決め手は?
三枝様:初めてSotas工程管理のカンバンに出会ったのはまだ開発途中の状態でしたが、ホワイトボードみたいなグラフィカルなカンバンは感覚的にわかりやすいなと。現在私たちが紙に印刷して掲示している生産計画と、見た目が大きく変わらないことに可能性を感じました。
というのも、私たちは導入を決めるポイントとして「現場がいかに楽になるか」という点に主軸を置いていたからです。いざ導入しても、結局現場が使ってくれないことには意味がないですよね。当社は年配の従業員も多く、その点は慎重に検討しました。いかに現場になじみやすいか、どれだけアレルギーなく活用できるか、そして導入した結果、業務が少しでも楽になれるかが大きなポイントでした。「楽になるなら使ってくれるだろう」、でもさらに手間が増えるとか、現状よりプラスの作業に感じられたら、きっと浸透しないだろうと。Sotas工程管理なら、現在の見た目を大きく変えずに導入できるのではないかと考えました。
吉元:ありがとうございます!私自身、起業してすぐに意識したのがとにかく現場に足を運ぼう、現場の声を聞こうということでした。プラスチック成形加工の会社様だけでも70社以上に訪問し、そして、直接現場の方からお話も伺って作ったカンバンですので、その部分もご評価いただけてとても嬉しいです。
導入サポートについて:打ち合わせを重ね、二人三脚で課題解決へ
質問③Sotas工程管理の導入までの当社のご支援はいかがでしたでしょうか?
三枝様:トライアルを始めてからは、当社とSotasさんが同じ川崎市ということもあり、週に1回ミーティングをさせて頂きました。投入するデータの整備などの苦労はありましたが、サポート頂けたのでありがたかったですね。またミーティングでは、使用して感じた疑問や課題などを伝え、「この課題はこのような運用でカバーしましょう」とか、「そのご要望はシステムの改修を検討します」などのやりとりを繰り返しました。
当然、私たちのすべての要望をシステムで解決できるわけではないのは分かっていますが、Sotasさんと二人三脚で課題の解決方法を検討する中で、少しずつクリアになっていく安心感がありました。
吉元:頂いたご意見は貴重なご意見(ユーザーボイス)として、週次で開発エンジニアを含めメンバーで話し合い、解決方法を議論していきました。私たちも機能のブラッシュアップを重ねている段階でしたので、大変ありがたかったです。
導入効果:生産計画に関わる材料・製品在庫確認の管理者工数が25%減
質問④Sotas工程管理の導入でどのような変化がありましたか?
三枝様:生産計画の立案ですね。従来は得意先様から受注を頂くと、まずはエクセルに打ち込み、その製品で使う材料があるかを現物確認し、材料がなければ発注する、という作業が毎日ありましたが、本格稼働時には25%の削減を見込んでいます。特に生産の起点となる材料在庫・製品在庫を把握できているのが大きいですね。
吉元:25%って結構ですね!それだけ皆様の負担を減らすことに貢献できていると考えるとさらに負担を減らすことができないか?という気持ちになっています。
三枝様:受注した製品を登録すると、製品在庫数を加味して「製品が○○個足りません」という表示がされ、そのまま生産も登録することができる。当然、製品在庫があれば「製品は足りています」と教えてくれるので、余剰な生産も減らせるのではと感じています。
製品在庫が足りない場合、生産を登録すると「材料が○○kg足りません」という表示がされ、材料発注の登録へ。
受注は登録したけれど生産スケジュールに入れ忘れた、スケジュールには入れたけれど材料発注に入れ忘れた、これまでヒヤリとすることもしばしばありましたが、やらなきゃいけないことを自然な流れで導いてくれているのはありがたいですね。
吉元:そうおっしゃっていただけて何よりです!今挙げていただいた生産現場のあらゆる数字を裏側で紐付けて、最適な道標を示すという部分、実は弊社の中でも開発をする中でもっとも悩んだ点でした。なぜなら、生産現場毎にそれぞれの習慣やクセがあり、それを吸収するにはどういった項目設定にするのが良いのかをずっと考え抜き、今の形になっています。ですので、そこをご評価いただけたことは弊社の開発エンジニアも嬉しいと思います。
三枝様:また生産が終わったら、材料在庫の使用した数を登録できるので、定期的な棚卸しを待つことなく、常に確実な材料在庫量を把握できるのは便利ですね。というのも当社は取り扱い樹脂の種類がとても多く、材料を探すのにも時間が掛かっていて。あるはずの材料が見つからなくて急いで発注したけれど、結局見つかったりなんてこともありました。
数字で把握することで「あの材料在庫は○kgだからきっとこのあたりにあるだろう」と目処が立てられるのは地味にありがたいです。
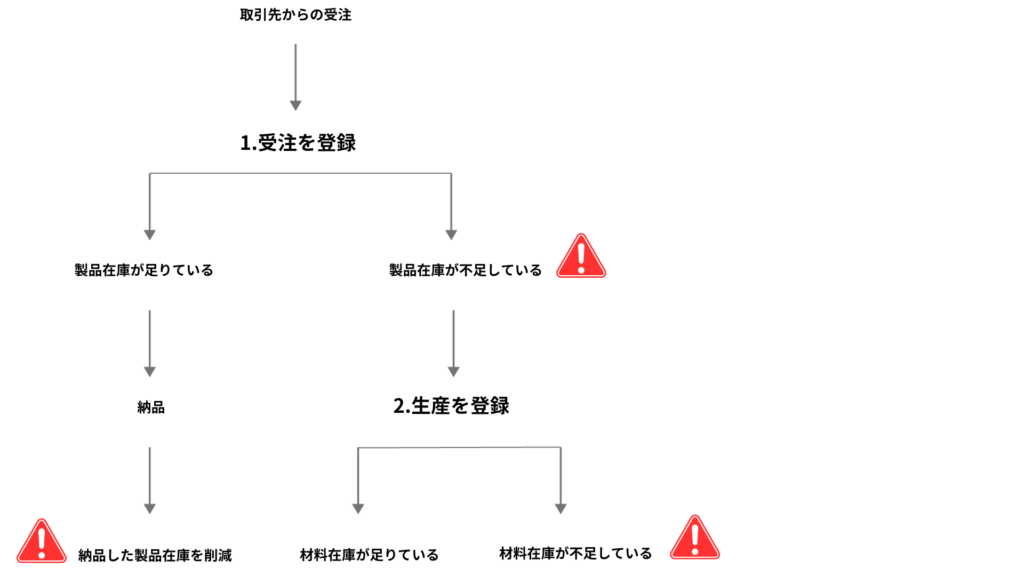
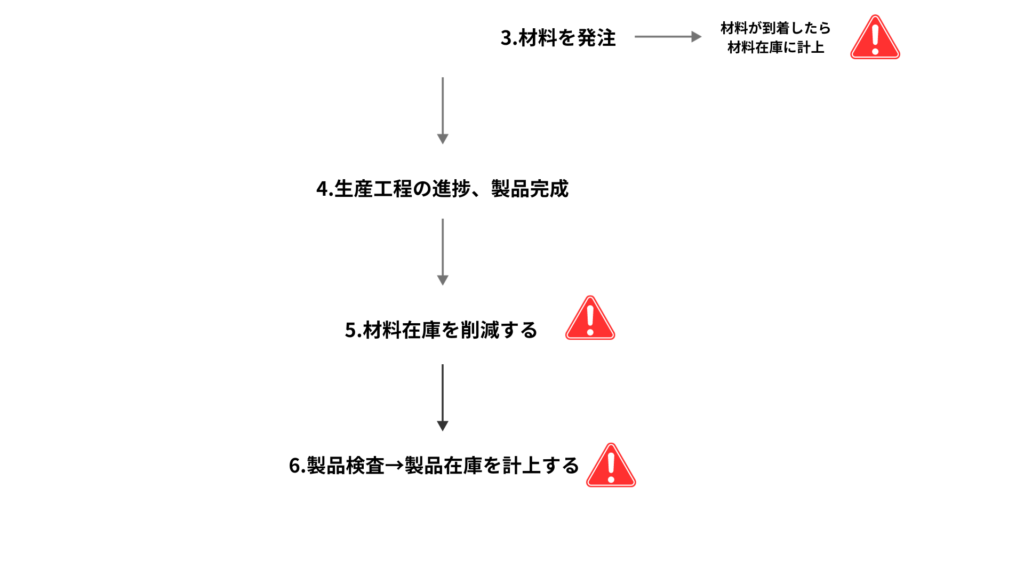
今後の利活用:技術者の日報や、製品ごとの歩留なども一元管理していきたい
質問⑤Sotas工程管理の利活用について今後の展望を教えてください。
三枝様:現場全員で使えるように、まずは土台をしっかり固めて、徐々になじませていきたいですね。従来はエクセルで作成した生産計画を印刷して貼り出していたのですが、先日、大きなタッチディスプレイを導入したので、そこにガントチャートを映してみんなで見られるようにしています。個人はカンバンを見て作業を進める、個人が手元のタブレットで生産カンバンを動かしたら、共有のガントも連動して、工場全体の動きが分かる。そうすると管理側も技術者も時間短縮につながりますし、みんなが少しずつ働きやすくなるかなと。
今後は日報や製品ごとの歩留などもSotas工程管理で一元管理していきたいですね。工場全体の効率化を進めることで、自分たちの本業であるものづくりに専念し「MADE IN TOHOPLATEC」の品質をもっと極めていきたいです。
吉元:三枝さん、ありがとうございました!ぜひ一緒に取り組んでいきましょう。引き続きよろしくお願いいたします。
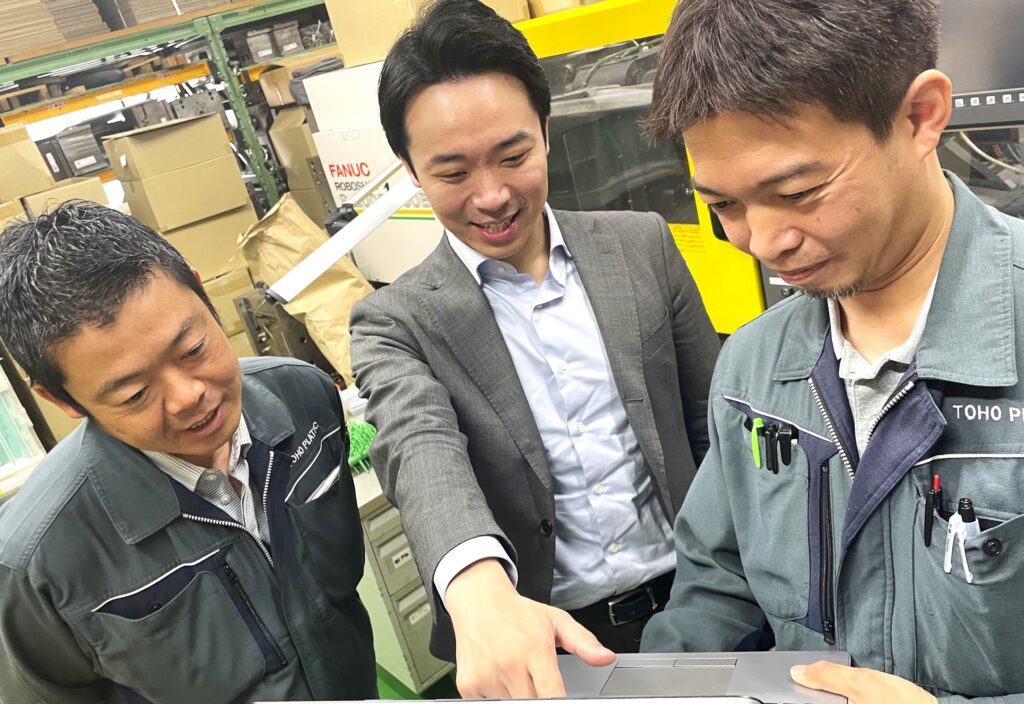
有限会社東邦プラテックは、外観に高い精度を要求するプラスチック射出成形加工を得意とする会社です。耐熱性のあるスーパーエンプラ樹脂の成形加工を行っています。