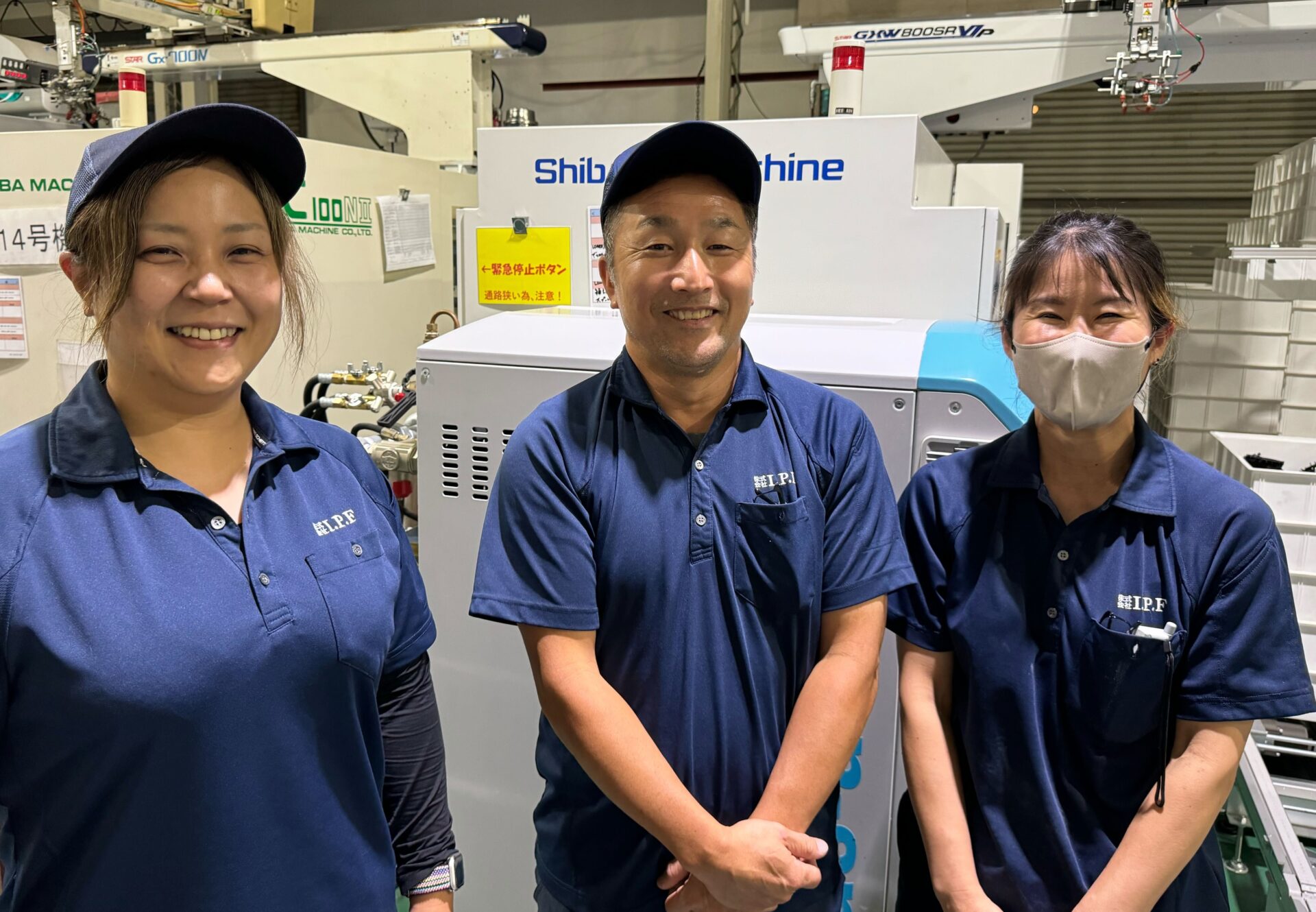
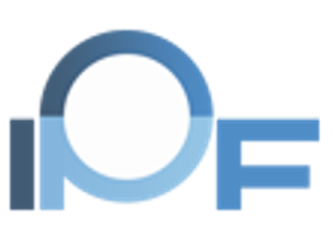
- 企業規模
- 20名-50名
株式会社I.P.F
代表取締役社長 飯塚 正師 様(中央)
生産管理 川口 藍子 様(左)
総務 佐々木 真美 様(右)
導入の背景:数十年かけて磨き上げてきたエクセル管理から進化するタイミング
Sotas吉元:導入に至るまでの課題や背景についてお聞かせください
I.P.F飯塚社長:きっかけは、銀行さんからのご紹介でしたね。当時私たちの工場の生産管理は、数十年かけて確立してきたエクセルをベースに行っていましたが、若いメンバーも増えてきたこともあり、より機能性が高く、今の時代に合った生産管理へ進化するタイミングではないかと感じていましたので、詳しい話を聞かせてもらいました。
また環境負荷物質の見える化や管理、生産性向上、自働化など、今後積極的に自社に取り入れたい要素と合致する部分が多かったというのも興味を持ったポイントでした。
Sotas工程管理に決めた理由:「横のつながりが持てる」生産管理システム
Sotas吉元:Sotas工程管理を選んだ決め手は?
I.P.F飯塚社長:今どのくらい生産が進んでいるか、どこかで問題は起きていないかなどをリアルタイムに確認できる、つまり「横のつながりを持てる」生産管理だと、初めてカンバン画面を見たときに直観しました。受注から生産へ、生産から検査へ、リードマン(※)から物流へ、カンバンを移動させて生産を進めていく、見た目がシンプルで感覚的にわかりやすく楽しい、ここは決め手になりました。
※リードマン:生産と検査の橋渡し役
Sotas吉元:自分の役割が済んだら、隣のレーンにカンバンをパスして、リレーのバトンのようにつないでいくイメージですね。
I.P.F飯塚社長:そうですね、私たちは「心をこめてパスを送る」と表現しています。それからもう一つ、最初に製品をご紹介いただいた際に、吉元さんが製品の機能についてはもちろん、会社のビジョンや製品に対する熱い思いを伝えてくださったことも決め手でしたね。私は、誰が作ったか、誰とつながるかが大切なポイントと考えていましたので、これだと感じ、さっそく導入に向けて社内メンバーと具体的に検討を始めました。
導入サポートについて:作りっぱなし、売りっぱなしではないサポート体制
Sotas吉元:導入サポートについてはいかがでしたか?
I.P.F飯塚社長:月一の頻度で、導入に向けて相談をしました。私たちのこれまでの運用方法と照らし合わせて、「Sotas工程管理でこれを実現したい」「このデータはこうあってほしい」などの意見にもしっかり向き合っていただき、時に私たちの要望を新しい機能としてアップデートしていただいた部分もありました。Sotasさんは、作りっぱなし・売りっぱなしではなかったですね。
Sotas吉元:Sotas工程管理で必要とされるのはどのような機能か、それはなぜ必要か、何度もヒアリングさせていただきました。私たちの方こそ、I.P.F様からたくさんの重要なヒントをいただき、ブラッシュアップできたと思っています。
どういう現場にSotas工程管理は向いている?:小ロット多品種には特に最適
Sotas吉元:Sotas工程管理はどういう現場に向いていると思いますか?
I.P.F川口様:カンバン方式の工場なら特に使いやすいのではないでしょうか。小ロット多品種だと動きも大きくわかりやすいですし、カンバンを次々と片付けていけるので、達成感もあるのではないかと思いますね。
I.P.F飯塚社長:私は変化に前向きな会社に向いていると思いますね。当社には、さまざまな成形企業さんが視察に来られるのですが、その際にも「これは何?」「これはなぜ?」と興味を持って質問してくださる会社は成長意欲が高く、前向きで、変化に対して柔軟です。Sotas工程管理は、そんな従来との違いを前向きに受け止められる企業さんには特に向いているのではないかと思います。
導入効果:現場への移動、大体月換算で1日分のロス削減
Sotas吉元:導入効果についてお聞かせください
I.P.F川口様:先ほどの話にもありましたが、「今リアルタイムでどのくらい進んでいるか」の確認に要する工数を削減できています。
これまでは通常私たちがいる事務所から工場、検査場、倉庫まで都度足を運んで確認しに行っていたので、その工数が掛かっていました。納品が迫っている製品の場合は、心配なので日に数回見に行くこともありました。確認だけなら電話でもよいのですが、電話だと作業員の時間を止めることになってしまうので、それは避けたいのです。
I.P.F佐々木様:当社では方針として、「1個、1秒、1歩のムダをなくす」という言葉を掲げており、工数削減については会社全体でもシビアに捉えています。
I.P.F川口様:今では工場でカンバンを移動させた、つまり生産が始まったことが事務所にいながらにして把握でき、また「今リアルタイムに現場でどのくらい進んでいるか」を確認することができ、安心できます。事務所・工場・検査場・倉庫の往来を考えれば、大体月換算で1日分のロスを減らせているという感覚です。
I.P.F佐々木様:川口は確認のため現場に行き、進捗が思わしくない場合、そのまま手伝いを始めてしまい、なかなか帰ってこないこともありますので…(笑)
I.P.F飯塚社長:気持ちはわかるけれど、「役を全うする、役を越えない」というのも大切だと考えます。ここで削減できた工数はスキルレベルアップに充てて、さらなる効率化、生産性の向上を目指していけたらと思いますね。これまでアナログを経験してきたからこそ、デジタルへの移行によってアイディアも出てきますよね。過去のやり方に囚われず、時代が何を求めるのかを事前に考え、チャレンジを繰り返し、世界一の生産工場を目指していきたいですね。我々の仕事は、「見えないものを見えるようにする・見えたものに心を添える・心を添えたものに付加価値を付けて届けること」です。これが実現できるのがSotasの工程管理システムだと思います。
Sotas吉元:飯塚社長、川口さん、佐々木さん、ありがとうございます。I.P.Fさんの世界一の生産工場への道のりに少しでもお役立ちできたら光栄です!これからも色々なアイディアや活用方法をお聞かせください。
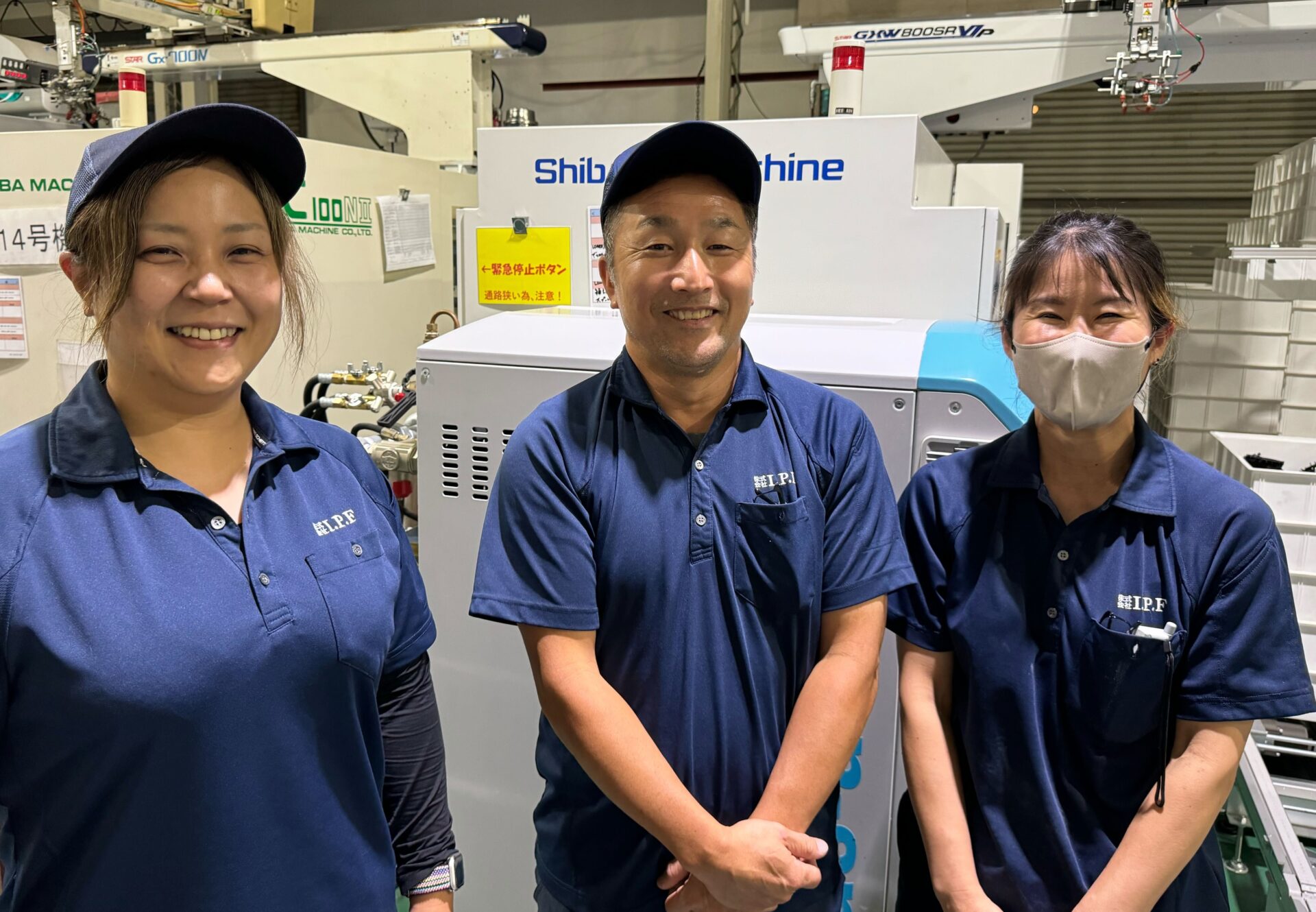
時代の変化とともに技術や取り巻く環境が目まぐるしく変わっていますが、わが社は「マーケティング」と「イノベーション」の精神で成長していきたいと考えております。
世界一の生産工場を目指して挑戦していきます。